From months to minutes in Arçelik collaboration
When you ship hundreds of millions of household appliances to more than 100 countries across several continents, even small gains in efficiency can have a dramatic impact on overall production. One of the most critical tests before household electrical products are sent to market is engineering validation tests of their power supply units. The power supplies in each unit, whether it be a television or refrigerator, need to be tested and depending on their final destination will need to be robust enough to handle fluctuations of the regional power grid. To ensure this is the case, all components that face electrical stress during power supply operation (including semiconductors, capacitors, and wire-wound components) are tested before products are shipped. These tests are currently most often carried out by hand with engineers measuring the specific properties of a product’s switching transistors at a given voltage and load, a process that can take anywhere from two weeks to one month. An industrial use case in the Eclipse Arrowhead project demonstrates how this time can be reduced to merely minutes.
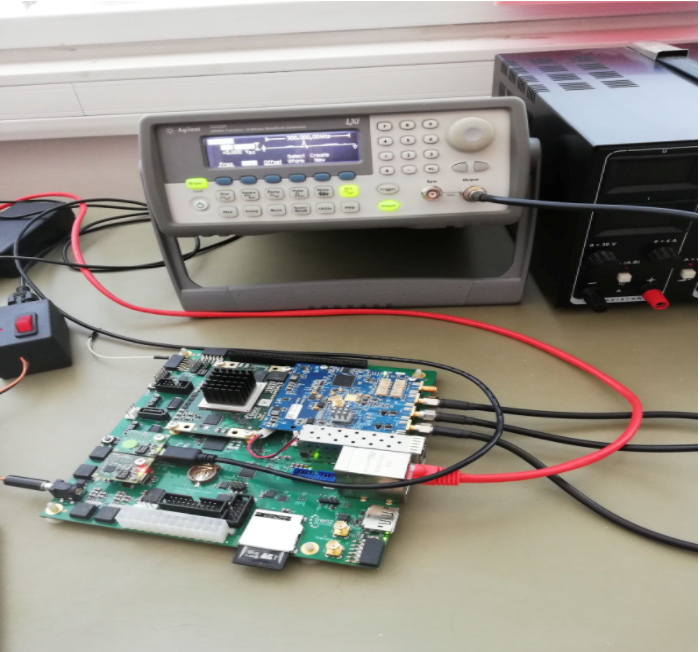
The collaboration involves Arcelik, one of Europe’s largest producers and suppliers of household electrical products, together with the Institute of Information Theory & Automation (UTIA), Prague, and the Institute of Electronics & Computer Science (EDI) in Riga, Latvia. All three collaborators are using Eclipse Arrowhead middleware to implement the current use case. Arcelik is a regular participant in European industrial projects and brings fifty years of experience producing and testing power supply units as well as an industrial testing environment to the project, which is monitored by researchers in Prague and Riga. Jiri Kadlec from UTIA explains that “in order to efficiently automate the testing process at Arcelik we need a giga-sample data acquisition system serving as an oscilloscope that is capable of analyzing what it is measuring and sending the analyzed data securely to an Eclipse Arrowhead cloud”. The result is a combination of an embedded processor and programmable logic on a single chip. This combination allows certain features to be accelerated. Steeply rising voltages or voltage overshoots could, for instance, be identified using software, but this would take a long time. Programmable logic accelerated hardware allows us to use an accelerated function to sort through the giga-sample and identify overshoots. And it does it as much as thirty three times faster than simply running software on the ARM processor.
This use case is not merely a research prototype and these efficiency gains are not theoretical. As Alper Özel, senior hardware design engineer at Arcelik, explains, “automating and digitizing these tests allows us to see this process and these products from a broader perspective, we can analyze and improve both the products and the process. It has a direct effect on the engineering process, reducing the time it takes by almost a month. This process generally takes two weeks to a month, but the old process is reduced to minutes with the implementation of his use case.” Özel points out that this reduction in engineering time is only one of the concrete benefits of implementing the new system. He clarifies, “from a broader perspective it also allows us to perform a more substantial analysis on our products on the market. When we ship the same products to Bangladesh, Africa, Turkey, Europe and Scandinavia these markets are all subject to different regulations. We have production plants in Bangladesh, India and Europe, and by implementing this same use case in those production lines, we will be able to develop a more comprehensive standard for the engineering phase of our power supply units. We can perform the same tests in all departments, collect more data and solve more issues.” To put this into perspective, Arcelik ships more than 300 million refrigerators worldwide, meaning that efficiency gains in one crucial area represents a significant saving of cost and human resources.
The system presented in this use case is currently deployed on off-the-shelf industrial grade carrier and sink solutions. The software consists of Linux together with interfaces to programmable logic controllers, an off-the-shelf analog device data acquisition card and relays that allow switching to different measurement points (prepared as a printed circuit board by Arcelik). This combination is used in testing at Arcelik and a simplified version is being used and tested in Prague at UTIA. In both cases these devices are connected by secure gigabit internet connectivity to a local cloud and are compatible with Eclipse Arrowhead services. The data providing clients are running on ARM devices supported by drivers and hardware logic to create two channels of one gigasample per second of 12-bit resolution data acquisition. This case provides an opportunity to further develop Eclipse Arrowhead edge technology with resource constrained devices as well as an opportunity to explore hardware acceleration and faster data acquisition through programmable logic. The intention is to go over to automated local clouds, so that measurements can be carried out independently via clients with a graphical user interface that will allow local users to set what measurements they would like carried out (in terms of load and voltage) and to analyze if the device is robust enough for the intended conditions or not.
While the project collaborators acknowledge that there is still work to be done on the software development side and local edge embedded software support, the system is already based on industrial grade printed circuit board modules used in Europe. The hardware carrier and the circuit boards are all manufactured for industrial production in Europe and the system is already in use at industrial grade. The current set up includes a GUI that allows users to set the number of tests and the parameters for those tests (e.g. a certain number of tests at specific voltages and a given load), collect individual sequences of data measurements and post-process them on a PC or process them directly on ARM processors. In explaining what the next steps are, Alper Özel says “The prototype phase is almost complete. In terms of electrical performance it does its job and is sufficient even if there is room for tinkering. The next phase is to redesign the testing equipment so that it is suitable for mass production with a clear life-cycle, so that it can be implemented with clarity in terms of planning and budgeting.” And Özel assures us that this will become a reality, “we will definitely do this, this is a very efficient project”.